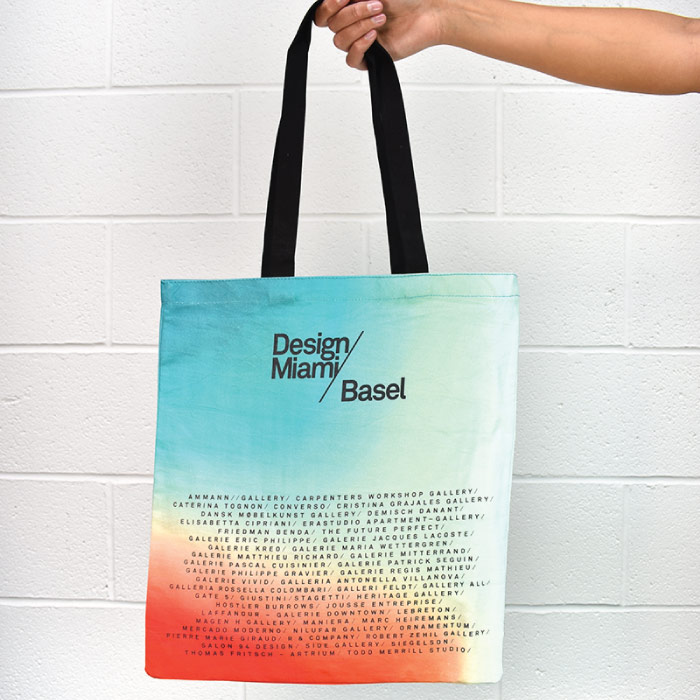
How are bags made?

A comprehensive guide to making a bespoke bag.
Starting your first bag project can feel like a huge task, an exciting adventure or complicated and could leave you unsure on where to start, which is probably why you are here! Let us help you with this simple guide that will outline each stage of the bag manufacturing process that leads to delivery of your bag.
Each stage cannot be finished until the previous one is complete. It’s a bit like a board game and your bag is the finish line! Here’s how to make a bag.
Our experienced team in Somerset, UK are a great bunch of people who have been making bags for many years. Chances are that one of us will have made the style of bag you are interested in making and will apply our knowledge to your project. If we’ve not made a concept you present to us, then no problem! Let’s try it and we’ll enjoy it.
1. Sketch
Rough around the edges or refined by a designer
Every bag project starts with a sketch or mood board that includes bag inspiration and preferences. To make a bag you may have a bag you want to replicate and make your own? This started off as a sketch at some point.
You can send us a rudimentary drawing of a bag that is annotated to explain what it is you are looking for and we can formalise that for you with a design visual that incorporates suggestions and alternatives if required.
Other considerations at this stage include defining what the bag is for, what will its purpose be? Who will use it? This is the foundation of an idea that helps determine the best fabric for the bag or the best fastening to close the bag.
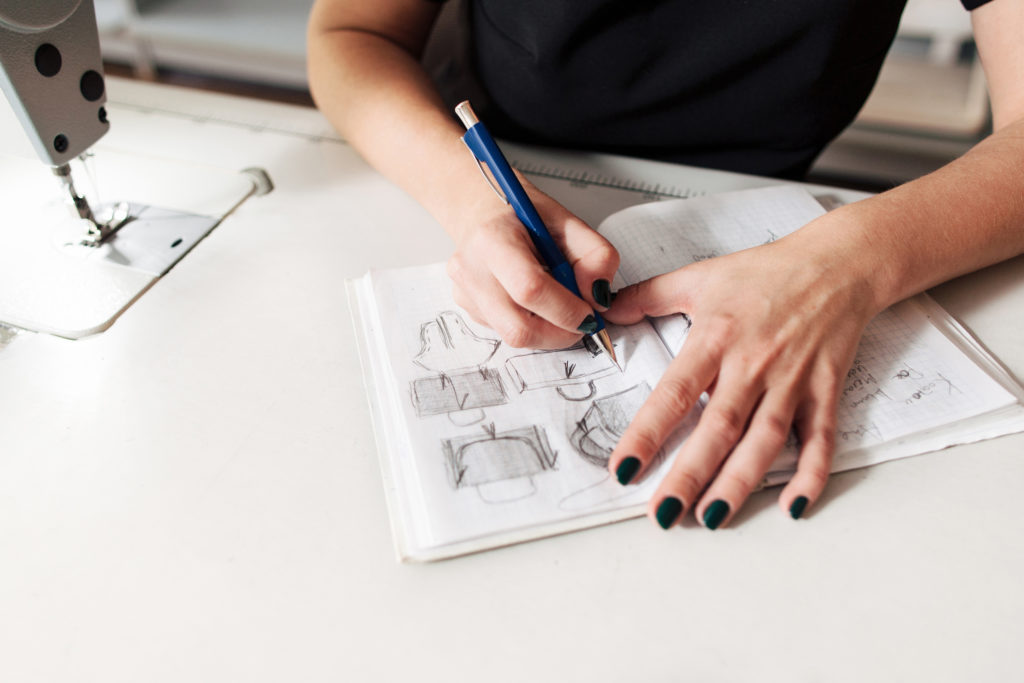
2. Components and fabric selected
Bag hardware and closures considered
- Working out what the bag will look like, the size it should be, how it should be closed, and the length straps then moves into what type of fabric will the bag be made from? What kind of straps will it have? PU or cotton webbing? Will there be one or two straps and are they long or short or both?·
- Fabric choice will be determined by purpose of the bag and your budget. You might choose Fairtrade organic cotton for a planet-friendly bag and you can choose from a range of weights starting at 4oz and going up to 24oz but your budget might only lend itself to a mid-range weight. The heavier and thicker the fabric, the more expensive it is.·
- Hardware is also considered at this stage. Are there buckles on straps to close the bag? Branded metal poppers or Pantone matched poppers to close a pocket?
When these elements are all initially selected then we can quote your project based on fabric required for the bag and number of units that you want to order plus the detailing.
3. Paper mould
Bag blueprint is created
So, you’ve worked out what your bag should look like, how big it should be and what it will be constructed of. Your project quote will be approved, and you’ve paid a deposit to launch your intention. We will then make a paper mould of the bag and work out where it should be folded, panels are measured, and seam allowances catered for. Positioning for zips and buttons will be allocated and a more accurate image of what your bag will look like in real life is created in paper. This is the bag pattern or blueprint for what happens next.
4. Hand sampling
A one-off sample is made by hand
After asking you questions in the first stage about what you want the bag for, what it should contain, the weight it should withstand and the size it should be, we will have gleaned enough information from you to quote the bag and sample it.
Before launching into manufacturing thousands of bags, we make a physical sample of the bag. It is made by hand, by our expert sample maker. She will order and cut enough fabric for two samples of your bag plus the other accessories required to make a pre-production sample of your bag.
When we’ve made the bag, we send it to you by courier.
The sample allows you to see the bag in the flesh. When you receive it, you can show it to your client to get their feedback. It’s essential that you use it to see if the desired contents fit correctly, put your phone in the phone pocket, hang it off your shoulder and see if they are long enough to sit on shoulders (put your coat on, try the bag out when you have a coat on as you’re likely to use it outside of your house), maybe the straps need to be adjustable and you’ve not thought about that before now).
It’s important to note that the sample is made by hand and not in a production line or by machine which leads to consistency across larger quantities. It’s also important to note that the fabric or hardware used for the sample will be one-offs. It will be the same fabric type, for example it could be a 7oz natural cotton. It will be ordered and cut from a 7oz cotton reel, but only enough for the sample. The fabric in the full production will be from a different batch and very slightly different or the hardware may be marginally different due to it being bought in a larger batch for the full production and the sample being made from one offs bought at market for the sample stage. Most fabric is from a natural source and even synthetics are made in batches and therefore pre-production samples can differ from full production very slightly.
Dye swatches
In some cases, fabric is Pantone matched. We will sample the bag in a stock colour and send you swatches of fabric dyed to a Pantone reference. You will choose from the swatches your preference in colour, the one you think is closest to your Pantone reference. It’s your choice.
Dying fabric can take 6-8 weeks. If you haven’t got this long and need you dyed bag sooner, we can over print fabric and colour match so the outside of the bag will be the desired colour and the inside of the bag will be white.
5. Design revisions
Amendments following evaluation of the sample
Sometimes at this stage, small adjustments are made to get the final bag right. Pockets may be made bigger or smaller on a tote bag, the depth of a gusset on a shopper bag may be increased in size or internal compartments may be added to organise the contents better. In rare cases, we sample again if the bag isn’t right first time. If we’ve got it wrong for example, then we’ll sample again for free. If you want to make big changes to the features of the bag, then we may charge you to sample again.
6. Fabric calculated for full order and sourced in quantity
On approval of the sample the fabric is sourced
The sample is prepared using the paper mould as a blueprint. Fabric is accurately calculated, and other details are also refined. If the bag has a zip, then the length of zip is defined and sourced in quantity. If the zip is Pantone-matched, then it will be manufactured at this stage. If the bag has embossed poppers, then they will start their own production process ready to be assembled in the final bag construction. Woven labels, enamel badges or personalised zip pulls for bags will be also be manufactured at this stage, once the sample has been approved by you. Fabric that is being dyed will begin now. The fabric is purchased and sent to the dying mill and is dyed to the colour swatch approved by you. It is dried, prepared and then rolled up and sent back to us in the factory ready to be cut out in the next stage.
7. Fabric pattern cut out
Pattern for every panel is created
When we receive the fabric that has been ordered in bulk, the pattern template is created for the cutting machine and the fabric is cut out and monitored by a member of the team. This guarantees accuracy and consistency across all bags from our minimum quantity of 250 to larger quantities of 10,000+.
The bag may have many panels, so each panel will be cut out to size, each with a small margin to allow for sewing together. An A4 tote bag will have two panels, a front and back panel. A larger shopper bag will have the same front and back panels seen in a tote bag, but also a gusset and side panels that also need to be cut accurately, with their correctly sized margin to allow for seams during construction.
8. Print and decoration on individual panels
Bag panels being printed are sent to the decorator
Now the panels are cut to size, they are sent to the to printer or decorator.
The relevant decorator accepts the artwork to be interpreted onto the panels as an EPS file, as well a visual for reference that includes Pantone colour references.The panels are decorated in accordance with the specification and then sent back to be constructed.
9. Production line planning
Factory schedule includes your bag project
Alongside the decoration of the bag panels and sourcing of accessories for the bag, production line scheduling will be taking place. The number of units in the order, the steps involved in constructing the bag, how long the print or dying will take plus the deadline for delivery will be considered. Working back from the desired delivery address, we will work out when the order will need to be packed, the quality control audit, right back to the bag being sewn together.
The number of sewing stations per bag will be determined, which sections will be sewn together and by how many people. Who will be sewing the badges on and where the zips are sewn in will all be considered when the job is slotted into production. There will be other bag projects being sewn together and at different stages of the process while your job is being processed so our production manager will be considering all of this while placing your job into production.
10. Individual component assembly
Fabric panels, zips, poppers and handles are prepared
By now, all elements for accessories for the bag that have been ordered, have arrived. Fabric is back from the dying mill, the printer has returned all printed panels, the embroidery is complete, and the hardware has arrived and been checked against the purchase order. All components are allocated to your bag project and stored in a holding area ready to be distributed to the relevant assembly stations on the factory floor.
11. Complete construction
All bag elements are pulled together
Getting all the elements of the bag together is a team effort. From the cutting of the panels and decoration to sewing it all together. It is done at assembly stations and by a team of experienced people who have done it all before. There isn’t a bag they haven’t made. Each person has a blueprint for the bag and a template to follow. Each of the elements they have been tasked with has a best practise example to adhere to and will ensure the section they are working on will be precisely the same as that example.
12. First stage quality check and loose threads cut
Attention to finer detail is refined
The Quality Control Manager will be checking the first bags made off the production line for the initial check that the production process is working. Then assembly commences. Loose threads are cut short during the process and one of the quality team monitors progress as the order is assembled, there will be a checklist to work through that includes print direction, hardware in place, zips sewn in the facing the correct direction, handle length precision, reinforced handle stitching, linings included, pockets the right way around and on the correct panel and so on.
13. Quality control
Final checks prior to packing and shipping
Now all of the bags are constructed, the final quality control check will commence. The bags are complete and should include all elements within the specification. The Quality Control Manager and her team will inspect a proportion of the order against the check list. Random bags will be taken from the finished order and checked to ensure the bags are as per the described specification but also that they are finished to perfection. Loose threads and imperfect print will not be tolerated.
We use an internationally acclaimed external audit team to review assembled bags during production and prior to packing on orders of over 5000 units. You can have input on what you would like to be checked during an audit.
14. Ironing
Bags are steamed or heat pressed to remove creases
Now the order is complete and has passed quality control, the bags are ironed and folded for packing. Bags will be hung and steamed flat if required or folded in accordance with the order specification. You may have asked that the bags include a swing tag to be included during production and this may be added at this stage as the bag is prepared for packing so that the swing tag lies flat and protected during folding. You may have specified that the bags are left open if they have a closing mechanism to make it easier to stuff with contents when you receive them, this will be actioned at this stage.
15. Packing
Packing lists are created when cartons are loaded
As the bags pass through ironing and preparation stage, they are packed in accordance with the order specification. We pack our orders in protective compostable packing prior to going into the cardboard shipping carton which are predetermined sizes. Depending on the size of your bag, will depend on how many can fit in the compostable protective bags. The packing list provided with the order will outline how many units are in a carton and will sound something like this: 60 units per carton / 10 cartons (600 units in total). There would be 15 units per compostable bag in a carton of 60. The protective bag protects your order from getting damp in transit or picking up any nasty smells along the way.
We used to use plastic before we knew better. Now you will find your order wrapped nicely in a biodegradable bag that you can use in your food compost caddy and it will gently decompose and leave no trace.
15. Shipping
Bag order is in transit by sea or air
- We price shipping for orders of over 500 units to be shipped by sea. It’s cost efficient for you but also kinder to the environment. You can expect to see delivery take 5-6 weeks and the impact of sending it by sea is far less intrusive to the environment than sending it by air, which is quicker. We export shipping containers from India every 2 weeks and you can be sure that your order will shipped as soon as it becomes ready for dispatch. Once it arrives in the UK, then it is unpacked and checked then sent to our warehouse where we dispatch it by domestic courier to your allocated delivery address.
- If you have a larger order and would like a carton or two of bags prior to the whole order arriving, then we can arrange this. You can talk to your project manager about this.
- Some clients order large quantities of bags from us but don’t want the whole order at once. We can store in our warehouse in Somerset, UK and dispatch to you as required. We charge a small storage fee for doing this and shipping is charged at cost.
Something else you might have discussed with your project manager is our picking and packing service. You may have ordered bags from us plus other merchandise that needs to be packed with the bags prior to dispatching to your end delivery address. We can pick and pack all elements for you and ensure your recipients are receiving the elements you want them to.
So, there you have it. A guide to making a bag in quantities from 250+ to tens of thousands of bags. All bag projects are treated the same, whether you are ordering a smaller quantity or larger, quantity, you will receive the same attention and energy from start to finish. What are you waiting for? Email over your sketch or send us a list of your bag criteria and we’ll be delighted to make your bag.